Greencore Case Study
Greencore is a leading manufacturer of convenience food in the UK and their purpose is to make every day taste better.
Greencore supplies all of the major supermarkets in the UK with “Food to Go” and “Food for Later” products which includes ready meals, salads, sauces, sandwiches, and sushi. They also supply convenience and travel retail outlets, discounters, coffee shops, foodservice and other retailers.
They have 16 world-class manufacturing sites and 18 distribution centres in the UK, with industry-leading technology and supply chain capabilities. Greencore largely manufacture food products for retailers to sell as their own brand and have 150 product lines.
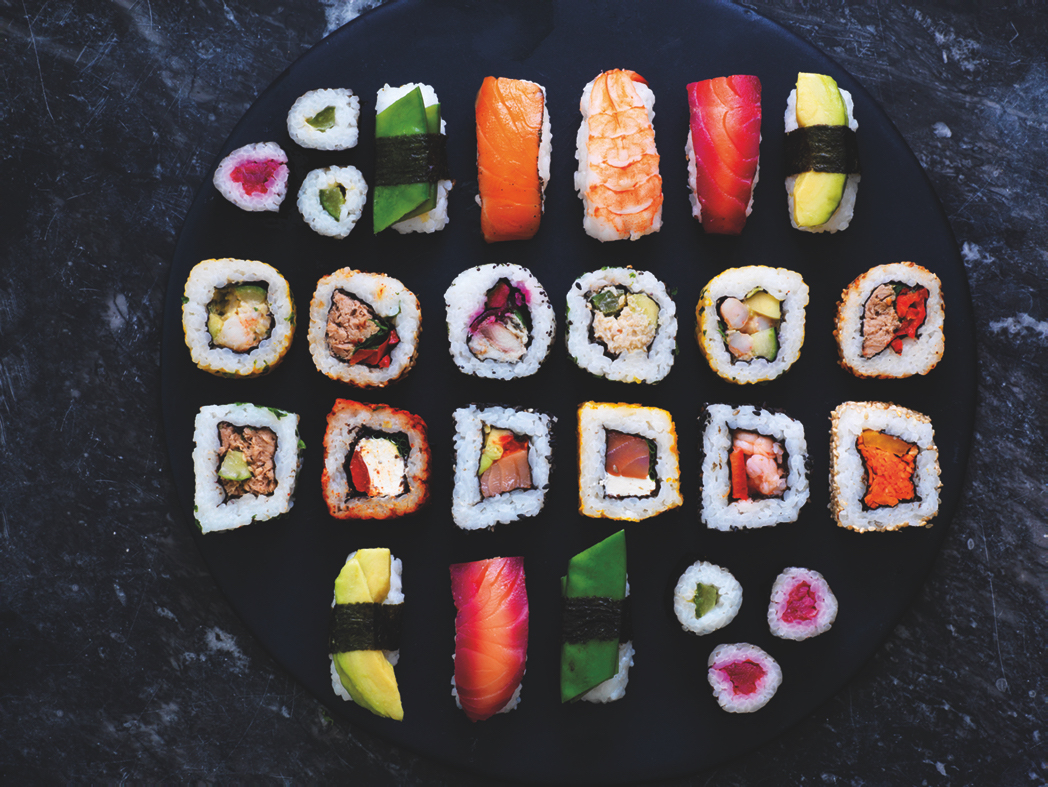
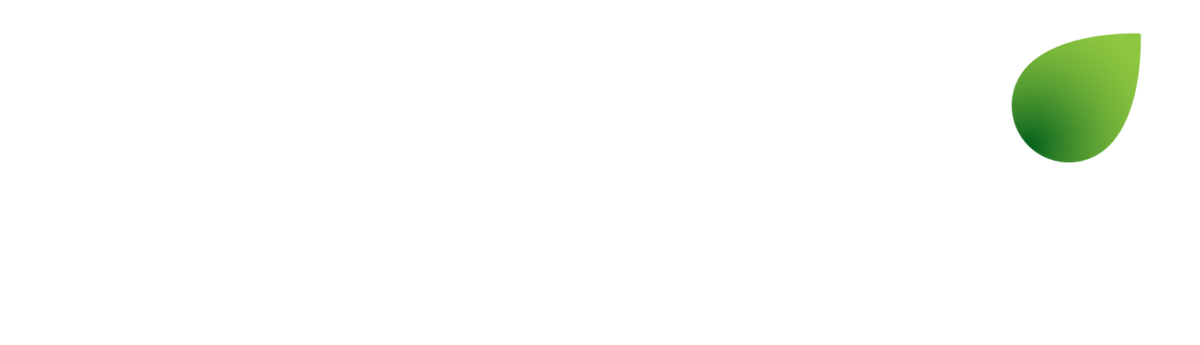
Business Challenge
Greencore has a model called The Greencore Way, which is built on the differentiators of People at the Core, Great Food, Excellence and Sustainability. Greencore strives for excellence in everything they do by building capability, driving efficiency and delivering value for all their stakeholders.
As a part of that purpose, Greencore started an initiative called GME – Greencore Manufacturing Excellence. The objective of this program was to improve efficiency of business processes, gain real time visibility of production lines and ensure any issues on the are addressed proactively. This helps Greencore streamline their functions and processes achieving cost and process efficiency which have benefits throughout the whole supply chain from manufacturer to consumer.
However, this was difficult to achieve with the existing manual processes, because:
Each line was checked manually by Line Controllers on the floor making sure that nothing was holding up the production.
The capture of line stats was a manual paper-based process with the results later being transferred to Microsoft Excel, adding time, resource, cost, and inaccuracy, and resulting in poor resolution times through the lack of real time feedback.
Each production line across the 16 manufacturing sites would record the progress information in Excel spreadsheets, which made it difficult to draw out any management information.
Solution
Having worked with and successfully delivered enterprise class Integration Platforms to Greencore IT Executive in previous roles, the Dot Group were approached to help resolve the challenges they were facing and support their manufacturing excellence initiative.
Dot Group built a solution for Greencore using IBM’s InfoSphere portfolio.
The platform was designed to measure key metrics on a manufacturing line, by extracting the production line data, applying business rules, and then presenting the data onto screens for Line Controllers and Operations Managers to make immediate adjustments to production.
The first implementation of this solution was completed for the “Food to Go” lines which is a full end to end assembly process of packaged sandwiches. The system collects data using a barcode reader on an existing technical system that scans the packaging and repurposes that data as count, efficiency and loss data and feeds that information into a system that is central for each site.
The efficiency of each line for a manufacturing site is displayed on a central dashboard.
Managers can drill in to view key performance parameters for each line. The KPI’s are classified under three main categories – Availability, Performance and Quality.
Each of these categories has further details that together give it a performance rating. Data from various manufacturing lines feeds into these dashboards and empowers managers to spot any inefficiencies and resolve issues straight away. They can be proactive in resolving issues, in-turn reducing any downtime and cost associated with it.
On the manufacturing floor, Line Controllers have been provided with the data management software and can see these dashboards on mobile devices and tablets. This improves accuracy of recorded data, reduces the administrative burden on the line engineers as they are not tasked with entering this data into excel sheets anymore. This also reduces the time taken to get the line performance data from the supply chain to the management dashboards.
Business Benefits
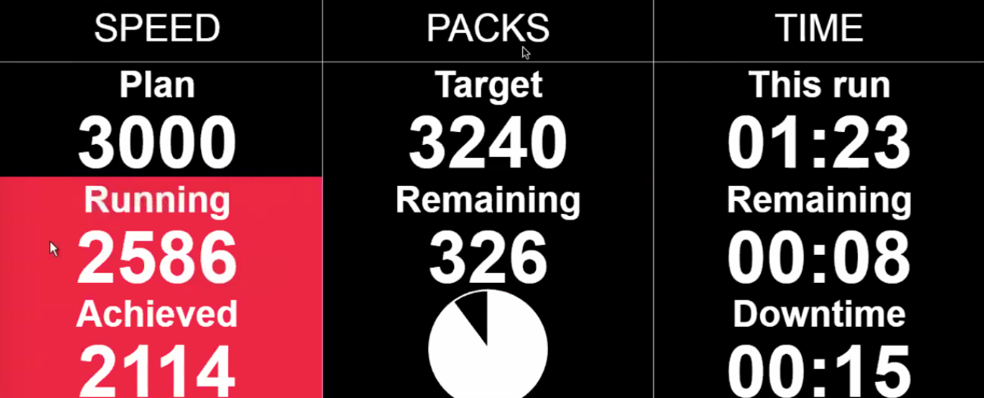
Know their data
The solution gives Greencore a near real time view of their manufacturing lines.
It helps them spot and resolve issues proactively.
They have seen significant savings in cost by reduction of down time and associated personnel cost involved in resolving these issues.
There are 100 Line Controllers who monitor the lines (70 on mobile devices, 30 desktops). This ensures data recorded is more accurate and reduces the time for data to reach the central database.
This project has contributed positively to saving Greencore about £2M in the past year due to improvement in line performance.
Trust their data
This has changed data from the lines into management information that is being used for better planning and production. Greencore also monitors how each line is adhering to planning.
Use their data
The central database enables them to use their data for further analysis using Qliksense.
Technical Nuances
There is a SQL server instance serving each line where status data is recorded.
Dot designed a data integration solution to collect the data from manufacturing sites and get all the data into a central database.
Dot also developed a custom solution exposing the new data as REST APIs Information Services Director to pull this data into a near real time view of the lines.
The line performance data is refreshed every minute.
This has enabled Greencore to use the data from the central database for other applications such as Qliksense.
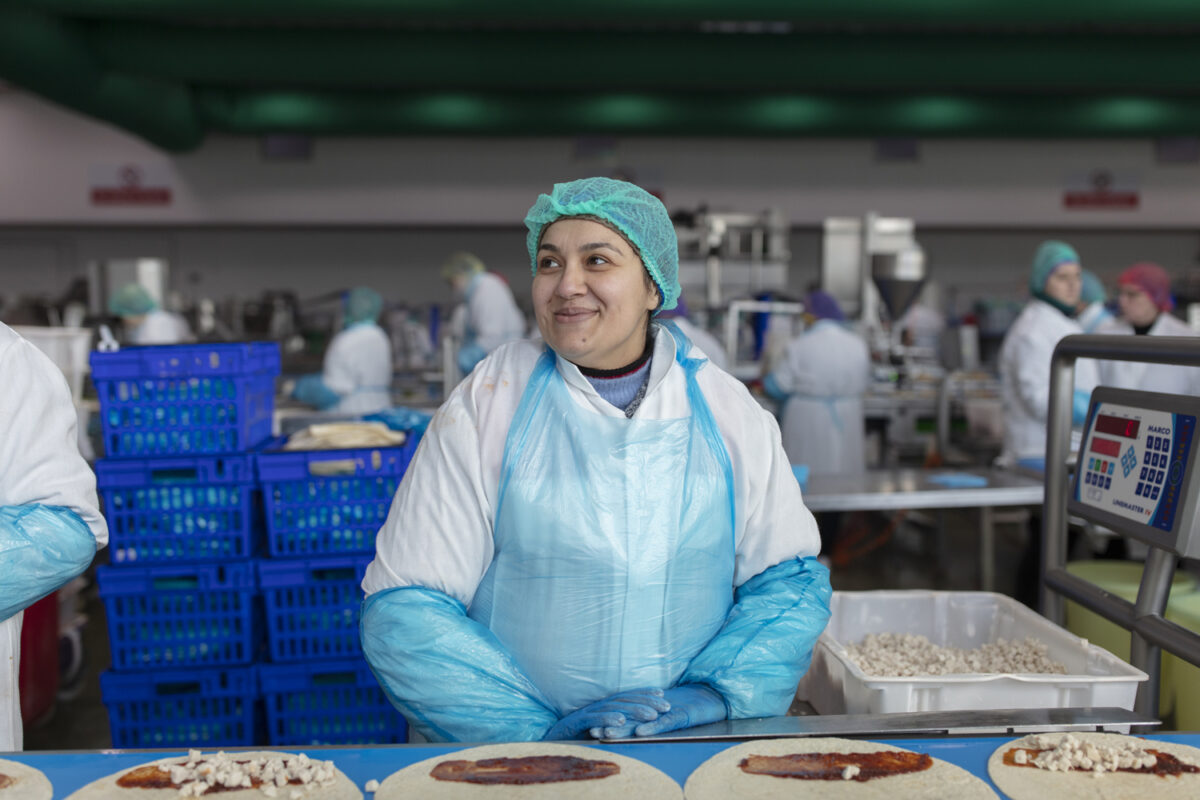
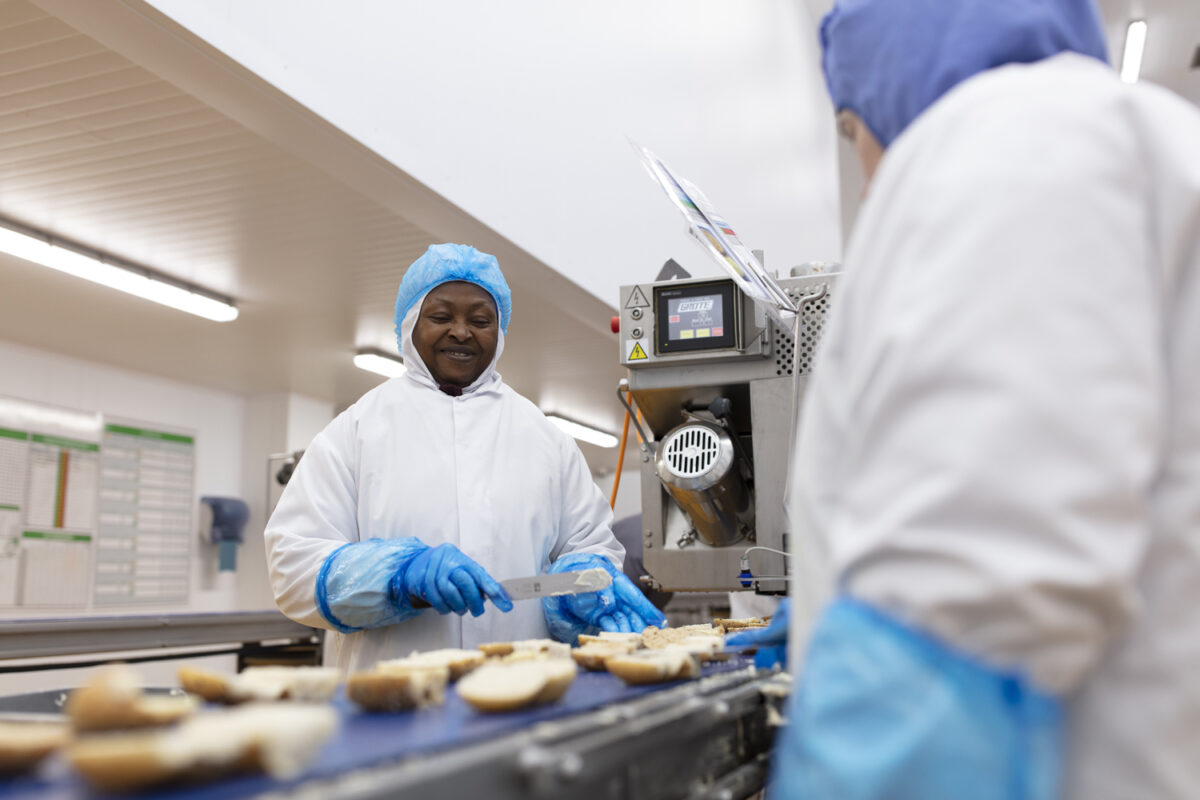
To find out more about Greencore follow them on social media or visit: greencore.com
Contact Dot Group to find out what we can to do help streamline your business, making it more efficient and effective.